Our AI-generated summary
Our AI-generated summary
HUM principal produtor de painéis à base de madeira atendendo principalmente ao mercado B2B, operando na Alemanha, enfrentou desafios significativos no fornecimento de ofertas de mercado competitivas e confiáveis, mantendo níveis adequados de eficiência operacional. A empresa produz vários tipos de painéis e sua estratégia de produção foi predominantemente de fabricação sob encomenda (MTO), o que resultou em dificuldades em atender às expectativas de nível de serviço devido à complexidade de prever a demanda e gerenciar os prazos de entrega.
O diagnóstico inicial revelou vários pontos problemáticos:
- Mix de estratégias de produção: A necessidade de melhorar os níveis de serviço redefinindo a combinação de estratégias de fabricação para estoque (MTS), fabricação sob encomenda (MTO) e acabamento sob encomenda (FTO).
- Ocupação de estoque: Restrições no espaço de armazenamento limitaram a capacidade de manter estoque.
- Falta de coordenação entre os tomadores de decisão: As decisões do programa de estoque pelas equipes de cadeia de suprimentos e marketing foram tomadas sem alinhamento ou sem uma plataforma compartilhada de apoio à decisão.
Para enfrentar esses desafios, foi desenvolvida uma solução de otimização de simulação, construída sobre um modelo de programação linear inteira mista (MILP). Esse modelo forneceu às equipes de marketing e cadeia de suprimentos uma ferramenta compartilhada baseada em dados capaz de sugerir estratégias de produção ideais para seu grande portfólio de produtos. Os principais componentes incluíram:
- Otimização das estratégias de produção: envolve a decisão de adotar uma estratégia Make-to-Stock (MTS), Make-to-Order (MTO) ou Finish-to-Order (FTO) para cada produto. Essas decisões garantem que a produção esteja estreitamente alinhada com a demanda do mercado e a eficiência operacional.
- Tamanhos de lotes e níveis de estoque: Modelo capaz de determinar tamanhos ideais de lotes e níveis de estoque esperados, ao mesmo tempo em que considera o congestionamento da fábrica e do centro de trabalho junto com os prazos de entrega esperados. Isso ajuda a equilibrar efetivamente o fluxo de produção e o gerenciamento de estoque.
- Análises hipotéticas: A capacidade de tratamento de vários cenários, juntamente com a parametrização de vários eixos, permite testar vários portfólios, combinações de produção e restrições operacionais. Essa flexibilidade é crucial para o planejamento estratégico e o gerenciamento de riscos.
- Algoritmo estratégico de produção: Empregado para otimizar indicadores operacionais e comerciais, respeitando as restrições operacionais inerentes. Devido à não linearidade do problema, foi escolhida uma abordagem de Programação Linear Inteira Mista (MILP). Essa abordagem separa a simulação das métricas de fila do algoritmo de otimização real, fornecendo uma estrutura robusta para otimizar os processos de produção. Uma arquitetura fácil de usar foi desenvolvida, integrada ao sistema ERP da empresa, com uma interface de parametrização que permite configurações fáceis de cenários e um resumo do KPI do painel fornecendo uma visão geral abrangente e uma análise detalhada no nível do material. Para garantir a adoção bem-sucedida, uma abordagem combinada foi usada:
- Mapeamento de processos: Um mapeamento completo dos processos de produção, cadeia de suprimentos e marketing foi realizado para entender o contexto dos negócios e identificar oportunidades de melhoria.
- Interface de parametrização: Uma interface personalizada foi desenvolvida para atender às necessidades de um vasto e diversificado grupo de partes interessadas. Essa interface permite a parametrização direta em vários eixos, como ajustar dados operacionais ou pré-organizar combinações estratégicas específicas. Ele é equipado com uma página de saída detalhada que complementa o painel de resumo do KPI.
- Implementação baseada na web: Uma interface amigável foi fornecida aos usuários finais, permitindo que eles interajam com o modelo de forma fácil e eficiente.
- Táticas de gerenciamento de mudanças: O treinamento de usuários foi implementado para promover a adoção autônoma da ferramenta. Isso foi acompanhado pelo envolvimento frequente das partes interessadas por meio de reuniões e sessões de treinamento. O feedback iterativo foi incentivado para promover a aceitação e o uso do novo modelo, complementado por pontos de contato regulares para abordar quaisquer preocupações e identificar oportunidades de melhoria.
Our AI-generated summary
Our AI-generated summary
A implementação do modelo de otimização de simulação produziu vários resultados positivos:
- Prazos de entrega aprimorados: A melhor utilização do estoque e os tempos de troca otimizados levaram a uma diminuição nos prazos de entrega propostos.
- Redução de custos operacionais: O aumento dos níveis de estoque da MTS, intensificado pelo aumento proposto no número de SKUs da MTS, resultou em menos trocas e menores custos operacionais.
- Gerenciamento efetivo de mudanças: A adoção do módulo foi facilitada por meio de várias táticas de gerenciamento de mudanças, garantindo uma integração suave aos processos existentes.
O projeto mostrou o impacto crítico da integração de modelos avançados de otimização de simulação com os sistemas ERP existentes no aprimoramento do planejamento da produção e da otimização da estratégia. Ao enfrentar os principais desafios e envolver várias partes interessadas por meio de um gerenciamento eficaz de mudanças, foi possível obter melhores níveis de serviço, reduzir os custos operacionais e obter maior controle e previsão sobre as estratégias de produção.
Este estudo de caso destaca a importância das ferramentas projetadas para interação multidepartamental, fornecendo visibilidade em toda a cadeia de valor, do chão de fábrica ao catálogo comercial.
O sucesso alcançado destaca a necessidade de combinar desenvolvimento analítico, mapeamento de processos e gerenciamento de mudanças para obter melhorias operacionais substanciais.
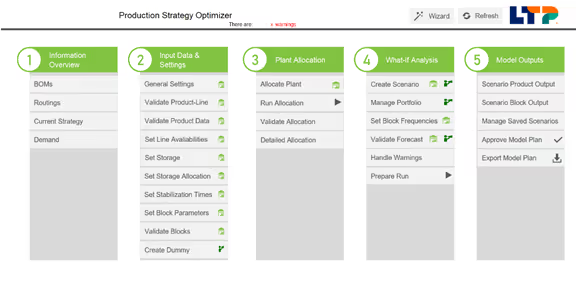
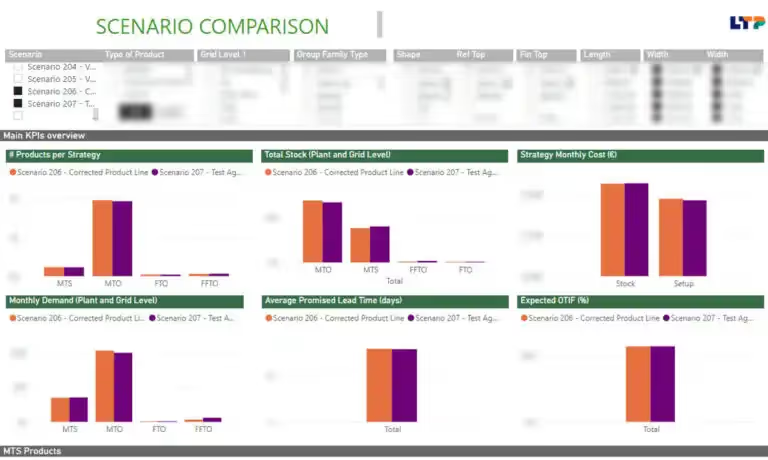