Our AI-generated summary
Our AI-generated summary
UN productor líder de paneles a base de madera prestando servicios principalmente al mercado B2B y operando en Alemania, se enfrentó a importantes desafíos a la hora de ofrecer ofertas de mercado competitivas y confiables y, al mismo tiempo, mantener niveles adecuados de eficiencia operativa. La empresa produce varios tipos de paneles y su estrategia de producción consistía principalmente en la fabricación por encargo (MTO), lo que dio como resultado dificultades para cumplir con las expectativas de nivel de servicio debido a la complejidad de pronosticar la demanda y gestionar los plazos de entrega.
El diagnóstico inicial reveló varios puntos problemáticos:
- Combinación de estrategias de producción: La necesidad de mejorar los niveles de servicio mediante la redefinición de la combinación de estrategias de fabricación para stock (MTS), fabricación por encargo (MTO) y acabado para pedido (FTO).
- Ocupación de acciones: Las limitaciones del espacio de almacenamiento limitaron la capacidad de almacenar existencias.
- Falta de coordinación entre los responsables de la toma de decisiones: Las decisiones sobre el programa de existencias por parte de los equipos de cadena de suministro y marketing se tomaron sin alineación ni sin una plataforma compartida de apoyo a la toma de decisiones.
Para abordar estos desafíos, se desarrolló una solución de optimización de simulación, basada en un modelo de programación lineal de números enteros mixtos (MILP). Este modelo proporcionó a los equipos de marketing y cadena de suministro una herramienta compartida basada en datos capaz de sugerir estrategias de producción óptimas para su amplia cartera de productos. Los componentes clave incluían:
- Optimización de las estrategias de producción: Implica decidir si se debe adoptar una estrategia de fabricación para stock (MTS), fabricación por encargo (MTO) o finalización según pedido (FTO) para cada producto. Estas decisiones garantizan que la producción esté estrechamente alineada con la demanda del mercado y la eficiencia operativa.
- Tamaños de lote y niveles de existencias: Modelo capaz de determinar los tamaños óptimos de los lotes y los niveles de existencias esperados, teniendo en cuenta la congestión entre la planta y el centro de trabajo junto con los plazos de entrega esperados. Esto ayuda a equilibrar eficazmente el flujo de producción y la gestión del inventario.
- Análisis hipotéticos: La capacidad de manejo de múltiples escenarios, junto con la parametrización de varios ejes, permite probar múltiples carteras, combinaciones de producción y restricciones operativas. Esta flexibilidad es crucial para la planificación estratégica y la gestión de riesgos.
- Algoritmo de estrategia de producción: Se emplea para optimizar los indicadores operativos y comerciales sin dejar de cumplir con las restricciones operativas inherentes. Debido a la falta de linealidad del problema, se optó por un enfoque de programación lineal de enteros mixtos (MILP). Este enfoque separa la simulación de las métricas de las colas del algoritmo de optimización real, lo que proporciona un marco sólido para optimizar los procesos de producción. Se desarrolló una arquitectura fácil de usar, integrada con el sistema ERP de la empresa, que incluía una interfaz de parametrización que permitía ajustar fácilmente los escenarios y un resumen de los KPI en panel que ofrecía una visión general completa y un análisis detallado a nivel material. Para garantizar una adopción satisfactoria, se utilizó un enfoque combinado:
- Mapeo de procesos: Se llevó a cabo un mapeo exhaustivo de los procesos de producción, cadena de suministro y comercialización para comprender el contexto empresarial e identificar oportunidades de mejora.
- Interfaz de parametrización: Se desarrolló una interfaz hecha a medida para atender las necesidades de un grupo amplio y diverso de partes interesadas. Esta interfaz permite la parametrización directa en varios ejes, como el ajuste de los datos operativos o la organización previa de combinaciones de estrategias específicas. Está equipada con una página de resultados detallada que complementa el panel de resumen de los KPI.
- Implementación basada en web: Se proporcionó a los usuarios finales una interfaz fácil de usar que les permitía interactuar con el modelo de manera fácil y eficiente.
- Tácticas de gestión del cambio: Se implementó la capacitación de los usuarios para promover la adopción autónoma de la herramienta. Esto estuvo acompañado de una participación frecuente de las partes interesadas a través de reuniones y sesiones de capacitación. Se alentó la retroalimentación iterativa para fomentar la aceptación y el uso del nuevo modelo, complementada con puntos de contacto periódicos para abordar cualquier inquietud e identificar oportunidades de mejora.
Our AI-generated summary
Our AI-generated summary
La implementación del modelo de simulación y optimización arrojó varios resultados positivos:
- Tiempos de entrega mejorados: La mejor utilización de las existencias y la optimización de los tiempos de cambio condujeron a una disminución de los plazos de entrega propuestos.
- Reducción de costos operativos: El aumento de los niveles de existencias de MTS, acrecentado por el aumento propuesto del número de SKU de MTS, se tradujo en un menor número de cambios y menores costos operativos.
- Gestión eficaz del cambio: La adopción del módulo se facilitó mediante diversas tácticas de gestión del cambio, lo que garantizó una integración fluida en los procesos existentes.
El proyecto mostró el impacto crítico de la integración de modelos avanzados de optimización de simulación con los sistemas ERP existentes para mejorar la planificación de la producción y la optimización de la estrategia. Al abordar los desafíos clave e involucrar a múltiples partes interesadas mediante una gestión eficaz del cambio, fue posible lograr mejores niveles de servicio, reducir los costos operativos y obtener un mayor control y previsión sobre las estrategias de producción.
Este estudio de caso subraya la importancia de las herramientas diseñadas para la interacción multidepartamental, proporcionando visibilidad en toda la cadena de valor, desde el taller hasta el catálogo comercial.
El éxito alcanzado pone de relieve la necesidad de combinar el desarrollo analítico, el mapeo de procesos y la gestión de cambios para lograr mejoras operativas sustanciales.
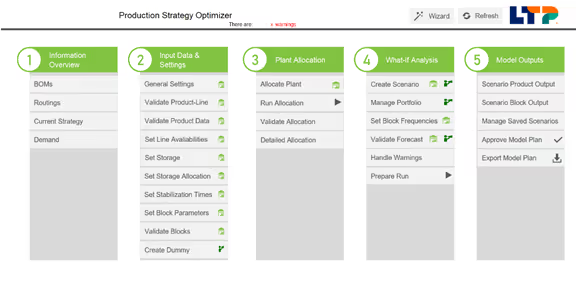
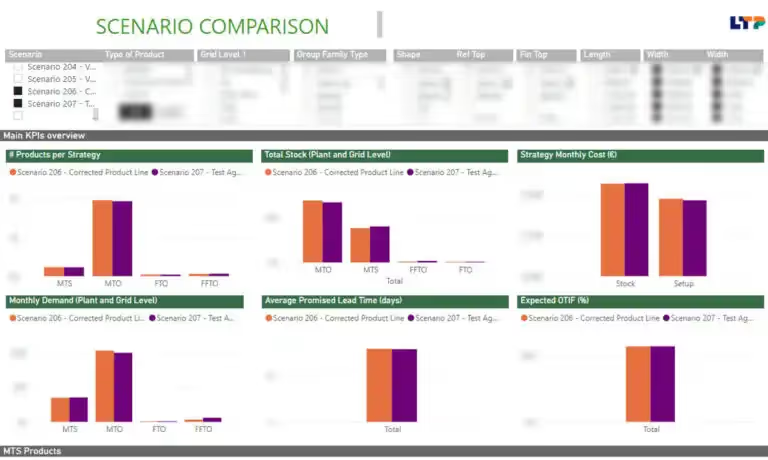