Our AI-generated summary
Our AI-generated summary
A leading Portuguese wine producer sought to consolidate production from two bottling centers into a single, streamlined hub to enhance efficiency and scalability for future growth. To meet the demands of an evolving market, the company required a flexible production facility capable of addressing current inefficiencies, overcoming bottlenecks, and adapting to changing product needs.
As consumer preferences shifted, the company recognized the importance of anticipating the impact of emerging product categories - such as carbonated, sparkling, and low-alcohol beverages - on production flow, ensuring the new facility could accommodate these trends while optimizing operations.
To solve this, the company partnered with LTPlabs, leveraging our expertise in process optimization. We began by thoroughly analyzing existing operations to identify inefficiencies and bottlenecks. Then, we anticipated demand and volume for the coming years, which later served as a basis for testing the scenarios.
With a clear understanding of the challenges, we developed four optimized facility layouts, each designed to streamline workflow and maximize efficiency.
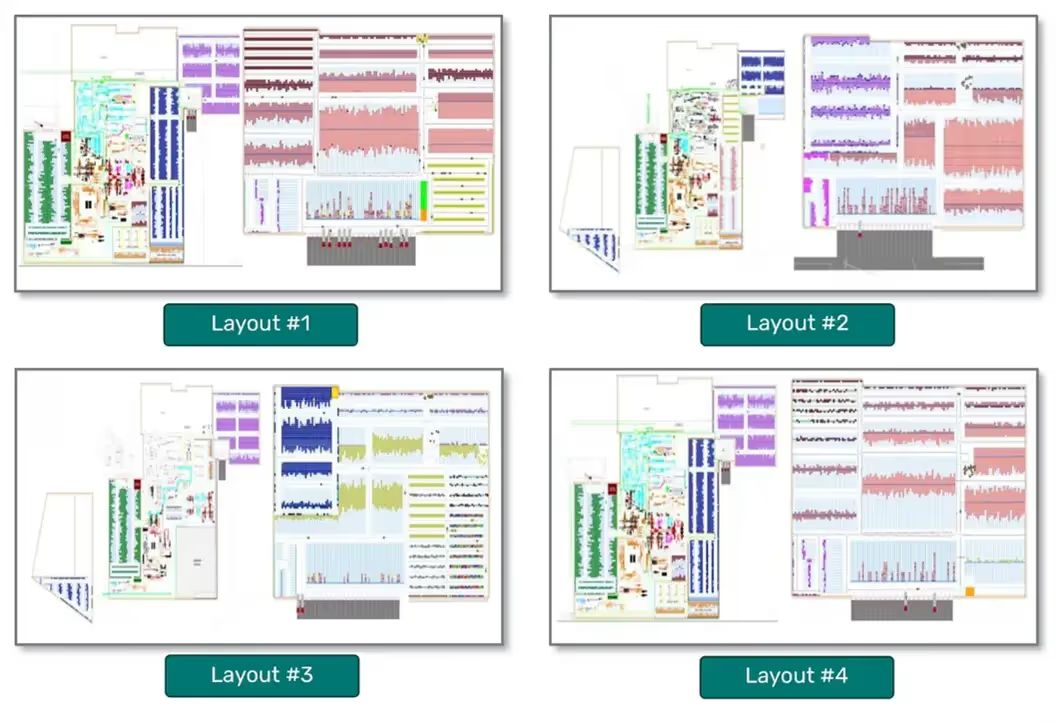
These layouts were then tested and refined using an AnyLogic simulation model. This served as a virtual replica of the FMCG production environment. The AnyLogic model provided a with a detailed view of operations within the facility without disrupting ongoing operations, which allowed to visualize and assess the performance of each design in realistic scenarios.
The model gave a clear view of the pros and cons of the designs of each facility layout. We tested how they would work over a day, month, and year, helping them predict the results.
In addition, we looked beyond the facility layout and explored automation options. By reviewing company's budget and goals, we found ways to simplify processes, reduce manual work, and boost production speed and accuracy.
Through this data-driven approach, we were able to select the most effective layout. The new design not only met current operational needs but also allowed for flexibility to accommodate future growth.
The project delivered remarkable improvements across key performance metrics:
- 30% increase in FMCG production throughput: The new production facility would significantly boost the production capacity.
- 25% reduction in lead times: Streamlined processes would cut the time required to produce and deliver goods.
- 20% improvement in resource utilization: Optimized workflows ensured better use of equipment and workforce.
- Enhanced flexibility: The new production facility layout allowed for quicker adaptation to changes in FMCG product demand.
This redesign of the production facility helped eliminate inefficiencies, while providing the company with the ability to adapt to changing market demands. With a scalable and more efficient operation in place, this wine producer is well positioned for continued growth and success in the competitive FMCG sector.
Our AI-generated summary
Our AI-generated summary